Exploring the Advantages of Cheap Plastic Injection Molds for Your Manufacturing Needs
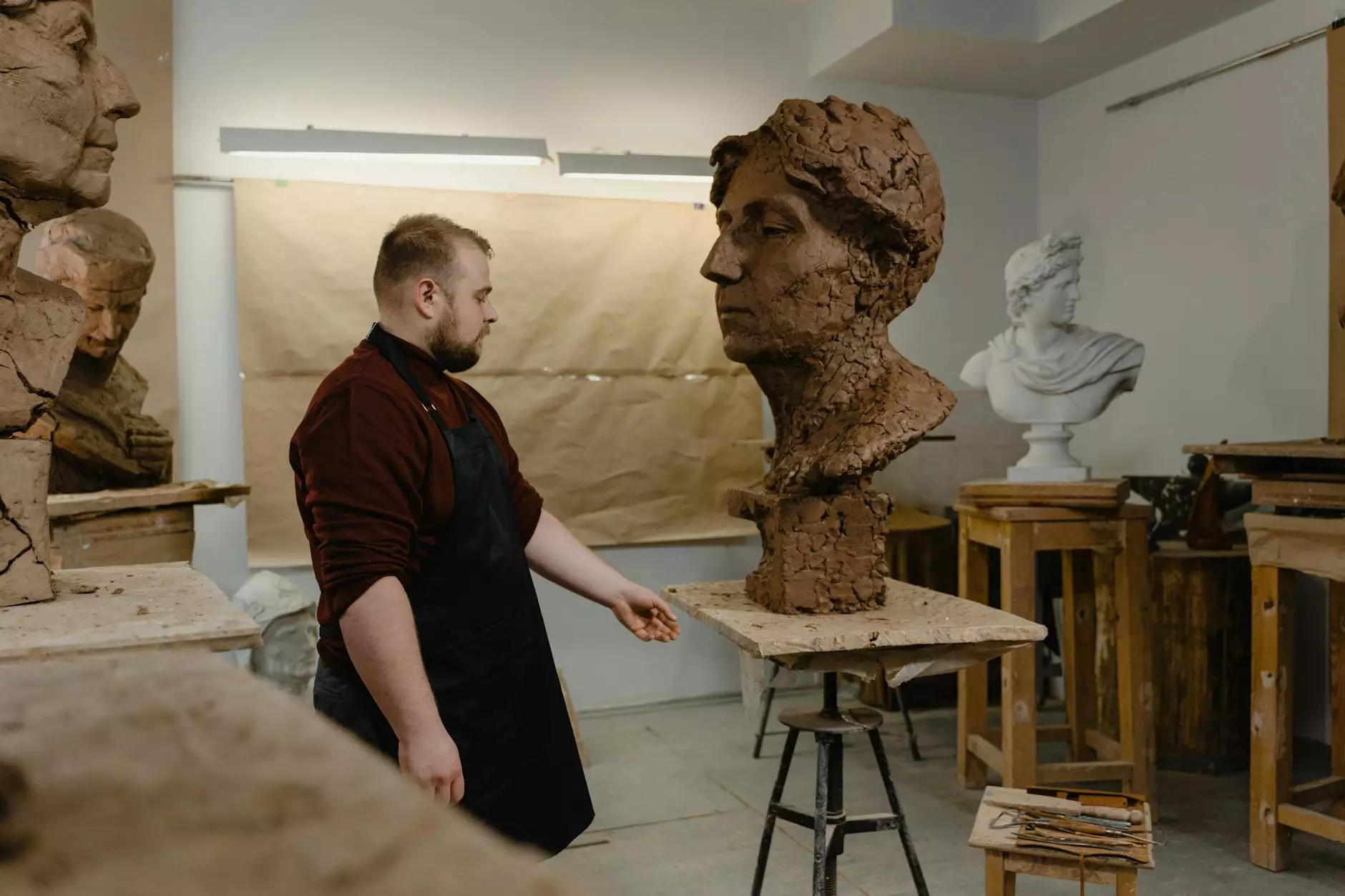
In today’s competitive landscape, manufacturers are constantly seeking ways to improve efficiency and reduce costs. One significant aspect of modern manufacturing is the use of cheap plastic injection molds, which can offer remarkable benefits for various industries.
What is Plastic Injection Molding?
Plastic injection molding is a manufacturing process used to produce parts by injecting molten material into a mold. The plastic injection molding process involves several steps, including:
- Heating: Plastic pellets are heated until they become molten.
- Injection: The molten plastic is injected into a mold cavity.
- Cooling: The plastic cools and solidifies in the mold.
- Ejection: The finished product is ejected from the mold.
Why Choose Cheap Plastic Injection Molds?
When it comes to molding plastic components, opting for cheap plastic injection molds can lead to significant savings without compromising on quality. Here are several compelling reasons to consider:
1. Cost Efficiency
One of the primary reasons manufacturers select cheap plastic injection molds is the lower cost associated with production. These molds are designed to be easily produced and replicated, which reduces the overall price. Here are a few ways that cheap molds can save your business money:
- Reduced Material Costs: Lower-cost materials can be utilized in the mold design, which decreases raw material costs.
- Faster Production Times: Cost-effective molds can be produced faster, speeding up the time to market for new products.
- Long-Term Savings: While the initial investment may be lower, the efficiency of cheap plastic injection molds can lead to significant cost savings over time due to the durability and life span.
2. Versatility
Plastic injection molds are incredibly versatile and can be used to create a multitude of products across various sectors, including:
- Consumer Goods: Toys, kitchenware, and household items.
- Automotive Parts: Interior components and exterior trim.
- Medical Devices: Various components essential to medical equipment.
- Electronics: Housings and protective casings for devices.
This versatility makes cheap plastic injection molds a valuable asset for manufacturers who need flexibility in their production line.
3. Customization
With the advances in technology, manufacturers can create custom molds tailored to specific product requirements at a lower cost. This includes:
- Design Flexibility: Adjusting the design to meet unique product specifications.
- Rapid Prototyping: Quickly produce prototypes for testing and validation.
- Color and Material Choices: Options to use various colors and types of plastics optimized for specific applications.
4. Increased Production Speed
Time is money in manufacturing. Plastic injection molding using cheap molds allows for quick production cycles. This increased speed leads to faster turnaround times for product delivery and helps businesses to:
- Meet Demand: Quickly respond to market changes and customer demands.
- Reduce Inventory Costs: Decrease the need for large inventories by producing just-in-time.
Potential Limitations of Cheap Plastic Injection Molds
While the advantages of cheap plastic injection molds are significant, there are some potential limitations to consider:
1. Quality Concerns
In some cases, cheaper molds can lead to less precise tolerances or lower durability. It is important to choose a reputable manufacturer, such as Deep Mould, that ensures quality in every product.
2. Material Limitations
Some cheap injection molds may restrict manufacturers to only certain types of plastics or materials, which can be a limiting factor depending on the desired product characteristics.
3. Long-Term Investment
While cheap molds can save money initially, they may not always remain the most cost-effective solution in the long run if they wear out quickly or cannot sustain high production volumes.
Best Practices for Implementation
To maximize the benefits of cheap plastic injection molds, manufacturers should consider several best practices:
1. Perform Thorough Research
Conduct comprehensive research on potential mold manufacturers. Ensure they have a proven track record of quality and reliability.
2. Collaborate with Engineers
Work closely with design and engineering teams to ensure the mold design aligns with product specifications and quality standards.
3. Invest in Testing
Before mass production, conduct thorough testing of prototype molds to identify any issues that can be rectified before full-scale manufacturing begins.
The Future of Cheap Plastic Injection Molding
The future of cheap plastic injection molds looks promising, with advances in technology leading to innovations in materials and mold design. Key trends impacting the industry include:
- Sustainability: Increased use of biodegradable or recycled materials in plastic production.
- Automation: Advances in robotics that can automate the molding process, improving efficiency and safety.
- Smart Manufacturing: The integration of IoT devices to monitor and optimize production lines.
Conclusion
Choosing cheap plastic injection molds can unlock significant advantages for manufacturers looking to reduce costs and improve efficiency. Understanding the benefits, limitations, and best practices can help companies make informed decisions that will enhance their production processes. For quality and reliability in the world of plastic injection molding, look no further than Deep Mould.
In conclusion, by leveraging the benefits of cost-effective plastic injection molds, businesses can remain competitive in the ever-evolving manufacturing landscape. Embrace innovation and ensure that your company is at the forefront of industry advancements, ensuring quality production and satisfied customers.