The Pivotal Role of Precision Injection Molded Plastics in Modern Business
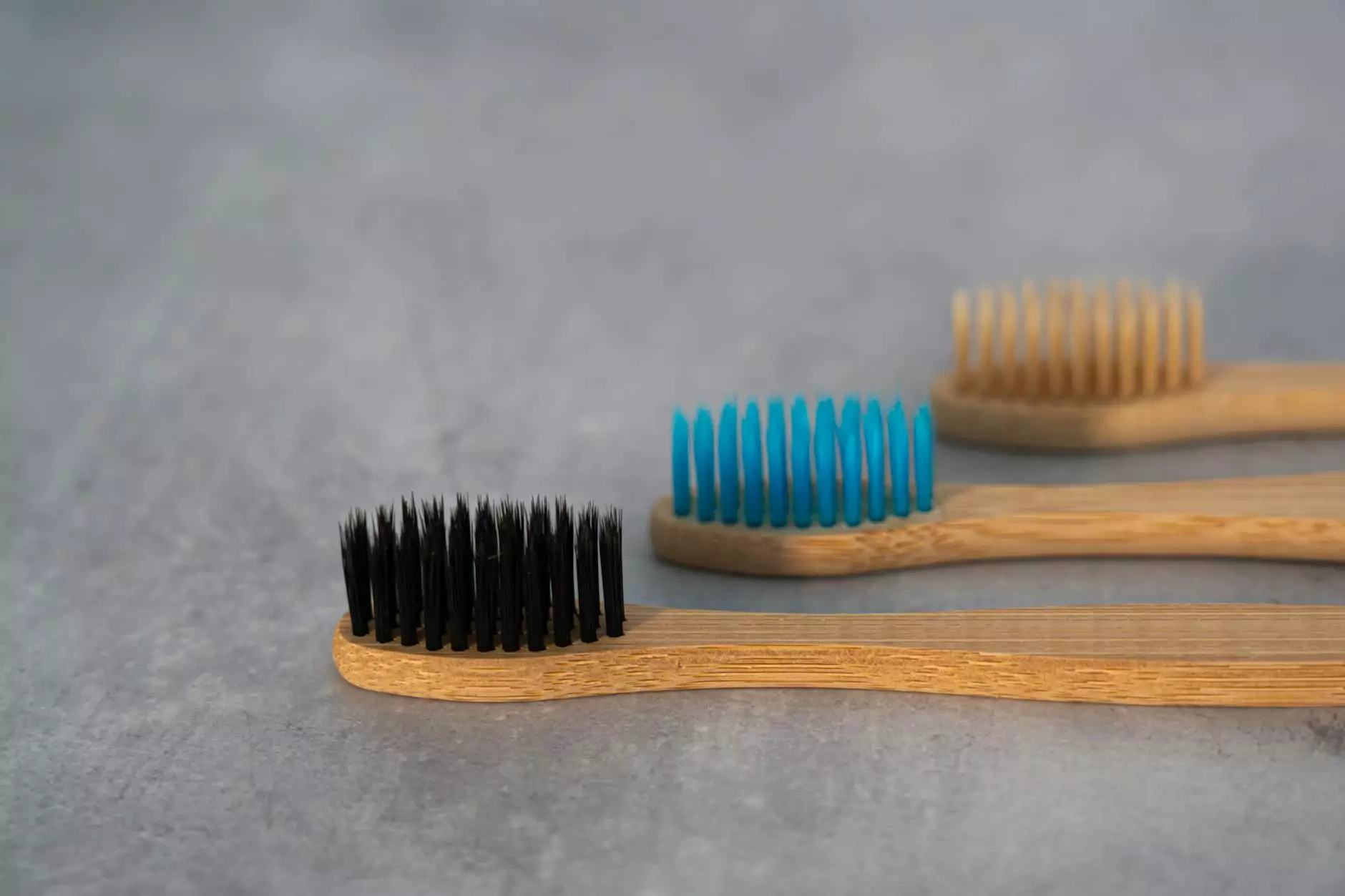
In today's rapidly evolving industrial landscape, the demand for high-quality manufacturing processes is paramount. Among these processes, precision injection molded plastics have emerged as a game-changer, enabling businesses to create components and products that meet the highest standards of quality and performance. This article delves into the intricacies of precision injection molding, its applications, benefits, and the profound impact it has on various industries, particularly in the realm of metal fabricators.
Understanding Precision Injection Molding
Precision injection molding is a specialized manufacturing process that involves the use of advanced machinery and technology to create highly intricate plastic parts. The process begins with the melting of plastic pellets, which are then injected into a mold under pressure. This method allows for the creation of complex geometries and tight tolerances, making it ideal for high-performance applications.
The Process of Injection Molding
- Material Preparation: Plastic resin is fed into the injection molding machine, where it is heated until it becomes pliable.
- Mold Creation: A custom mold is designed, typically made of steel or aluminum, to achieve the required shape and specifications.
- Injection: The melted plastic is injected into the mold cavity at high pressure, ensuring complete filling.
- Cooling: The plastic cools and solidifies, taking the shape of the mold.
- Demolding: The mold is opened, and the finished product is ejected, ready for further processing or assembly.
Applications of Precision Injection Molded Plastics
The versatility of precision injection molded plastics spans across numerous sectors. Below are some prominent applications:
1. Automotive Industry
In the automotive sector, precision injection molding is essential for creating lightweight, durable components. From dashboard elements to intricate engine parts, these molded plastics contribute to vehicle efficiency and performance.
2. Consumer Electronics
The consumer electronics industry relies on precision-molded plastic parts for devices such as smartphones, computers, and home appliances. These components not only enhance aesthetics but also improve functionality and durability.
3. Medical Devices
The production of medical devices requires strict adherence to quality and safety standards. Precision injection molded plastics are utilized to manufacture components such as syringes, casings, and internal device parts, ensuring reliability in critical applications.
4. Industrial Equipment
Many industrial applications incorporate precision molded plastics for components that must withstand rigorous conditions. These include gears, housings, and protective covers, all crafted to precision standards.
Benefits of Precision Injection Molded Plastics
Investing in precision injection molded plastics offers myriad advantages for businesses:
- High Accuracy: Injection molding allows for tight tolerances and intricate designs, ensuring that every part is manufactured consistently.
- Cost Efficiency: Once the mold is created, producing large quantities of parts becomes cost-effective, as the per-unit cost decreases significantly.
- Material Versatility: A wide range of plastics can be used, offering different mechanical and thermal properties suitable for various applications.
- Reduced Waste: The process is efficient, minimizing material waste compared to other manufacturing techniques.
- Scalability: Precision injection molding can easily scale up production without sacrificing quality, making it suitable for both small runs and mass production.
Metal Fabricators and Precision Injection Molded Plastics
For businesses in the metal fabricators category, understanding the synergy between metal and plastic components is vital. Many modern products integrate both materials, utilizing the strengths of each. For example, in creating housings for electronic devices, metal might be used for structural integrity, while precision molded plastics provide insulation and aesthetics.
Moreover, employing precision injection molded plastics can enhance the overall performance and durability of metal products, leading to innovative solutions in design and function. Fabricators can leverage these materials to provide lightweight alternatives to traditional metal parts, improving efficiency while maintaining strength.
Key Considerations When Choosing a Precision Injection Molding Partner
Selecting the right partner for precision injection molding is crucial for ensuring product quality and reliability. Here are some key considerations:
- Experience and Expertise: Look for manufacturers with a proven track record in your specific industry. Their familiarity with standards and best practices is invaluable.
- Quality Assurance: Ensure that the manufacturer employs stringent quality control measures to maintain consistency and adherence to specifications.
- Technology and Equipment: Advanced machinery and technology are essential for precision. Check if the manufacturer uses state-of-the-art equipment.
- Custom Solutions: Your partner should be able to provide tailored solutions to meet your unique requirements, including design support and prototyping.
- Scalability: Choose a manufacturer that can scale production based on your needs, from prototypes to full-scale production runs.
Future Trends in Precision Injection Molding
The landscape of precision injection molded plastics is constantly evolving, driven by technological advancements and changing market demands. Here are some future trends to watch:
1. >Sustainability
As sustainability becomes a paramount concern globally, manufacturers are exploring biodegradable and recycled materials for injection molding. This shift not only meets regulatory requirements but also appeals to environmentally conscious consumers.
2. Automation
Automation and robotics are set to transform the injection molding process. By incorporating automated systems, manufacturers can improve efficiency, reduce labor costs, and enhance precision.
3. Smart Manufacturing
The integration of IoT and smart technologies into injection molding will enable real-time monitoring and optimization of the manufacturing process, leading to better quality control and reduced downtime.
4. Advanced Materials
Research into advanced materials, such as composites and specialized plastics, will expand the applications of precision injection molding, particularly in sectors like aerospace and medical technology.
Conclusion
In summary, precision injection molded plastics play a critical role in the success and innovation of modern businesses across various industries. Understanding the intricacies of this manufacturing process can empower companies, particularly those involved in metal fabrication, to leverage the advantages of molded plastics effectively. As trends continue to evolve, embracing these technologies will pave the way for new opportunities and solutions in the market.
For businesses looking to stay ahead, partnering with expert manufacturers like deepmould.net can provide the edge needed for success in a competitive landscape.